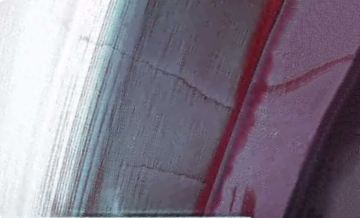
Item:
- A 250 MW turboalternator in a European power station
Problem:
- Inspection of the alternator revealed stress corrosion cracking in the 18Cr-5Mn retaining ring (end bell), consequent on storage conditions during overhaul
- Cost and delivery time of new end bell prohibitive
Approach:
- Identification of the cause of the stress corrosion cracking
- Evaluation of the possibility of removing the damaged area by machining off a complete ring of material, manufacturing a new ring and installing it by shrink fit
Outcome:
- Finite-element structural analysis of the end bell with new ring piece under the centrifugal loads generated at normal operational speeds confirmed the amount of interference required to ensure that the new ring will remain in place
- New ring piece manufactured, delivered to site and installed on the recently machined end bell
Benefits:
- Alternator returned to service with minimal downtime
- Cost effective solution implemented
- Propensity for future stress corrosion cracking reduced through changes in storage procedures