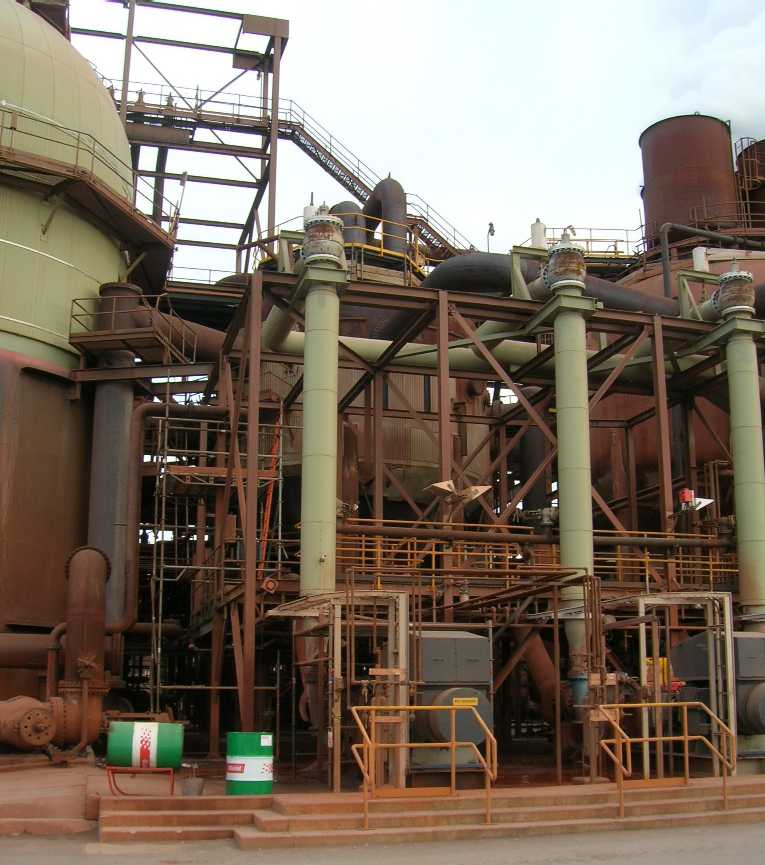
Item:
- 9m diameter blow-off tank in a European aluminium plant
Problem:
- Current cleaning practice for the tank interior involves personnel access, causing concerns for the plant health and safety management team
Objective:
- Safety team propose a tank modification utilising a 3m diameter nozzle on top of the tank, from which a hydraulic cleaning hammer can be suspended, so as to end the requirement for personnel access
- Can the nozzle support a 2.8 ton hydraulic cleaning hammer?
- Timescales for implementation both critical and short
Solution:
- Design of a supporting framework for the hammer and a structural integrity assessment of the framework/nozzle assembly

Results:
- In partnership with end user and manufacturing subcontractor, initial design of supporting framework proposed
- All operating loads identified and ideal position of entry to blow-off tank identified
- Safety factors agreed with end user
- Full structural integrity assessment performed
- Detailed sketches of final design provided for manufacturing process
Benefits:
- Design and structural integrity assessment performed in short timescales
- Manufacturing takes place within weeks of initial identification of requirements
- Reduced timescales results in cost effective solution for client
- New cleaning method successfully implemented