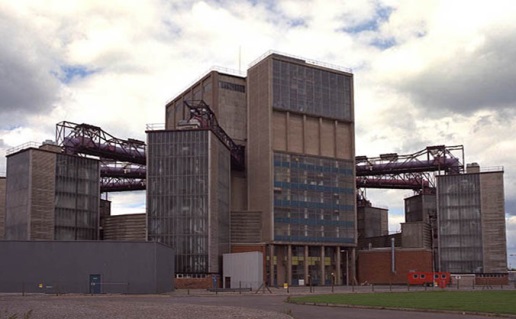
The subject plant had its boilers located external to the reactor buildings. This necessitated the primary cooling gas being conveyed in gantry-borne pipes with expansion bellows at critical locations. Fatigue issues led to bellows re-design as part of a life extension programme, in turn requiring replacement of the bellows tie-bars.
These tie-bars were intended to restrain bellows movement and the originals were fully-forged. As facilities to reproduce the original fabrication route were no longer available, an alternative had to be agreed between the operator and the regulatory authorities. It was considered essential that the replacement bars would not embrittle to an unacceptable degree in service.
A joint study was undertaken by the utility’s operations, construction and research divisions and the manufacturer. This resulted in agreement as to the relative mechanical properties of bars produced to the original procedure and to the proposed part-machined, part-forged route. Particular attention was given to the variation of properties through-thickness and to the susceptibility to in-service temper embrittlement. Consensus was reached as to realistic, achievable residual element limits in the materials specification and, following rigorous audit, the manufacturer’s quality plan and procedures were accepted by the utility.
The identification, acceptance and implementation of an alternative, cost-effective manufacturing route that could be implemented in a timely fashion allowed the life extension programme to be completed successfully.