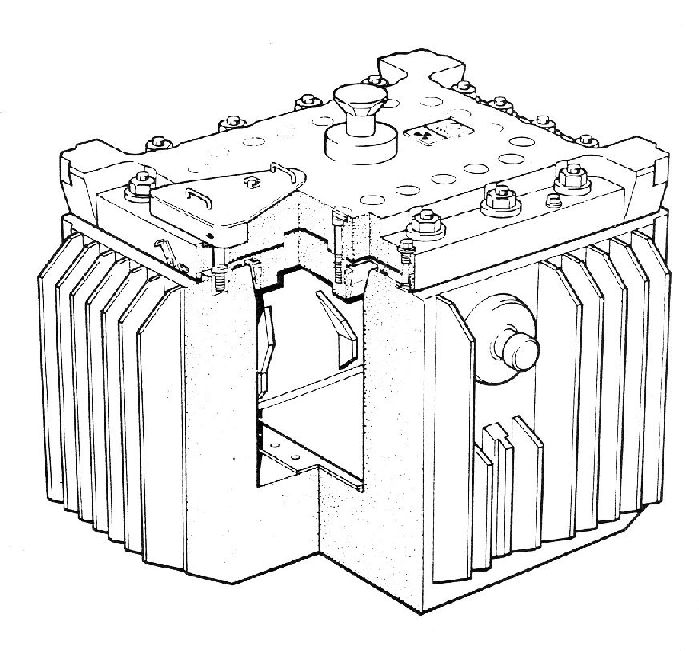
The objectives were
- to assess the performance of a nuclear fuel transport flask when subjected to a ½ hour 800°C all engulfing fire, to ensure compliance with International Atomic Energy Agency (IAEA) standards.
- in particular to address the integrity of the novel lid sealing mechanism and its ability to contain any release of contents.
A Finite Element (FE) model of the flask body, 2-part lid, holding down bolts and associated bolt nuts was created. The 2-part lid necessitated modelling the dual bolt tightening procedure, first one lid then the other. The model was validated by comparison of the FE results with those from a full scale pressure test.
The analysis was highly non-linear due to the presence of contact elements modelling interfaces between components, radiation and convection loads from the fire and the resulting elastic-plastic response of the flask.
A Cray super-computer was engaged for the analysis, and considerable runtimes were required.
The structure was predicted to reach 650°C and large parts were seen to respond plastically. Analysis confirmed the integrity of the lid sealing mechanism under the fire conditions modelled and temperatures at sealing locations were found to be within acceptable levels
This work confirmed the design without the need for an expensive fire test, which would have been difficult to control and monitor.
Sensitivity studies were performed on the input variables so as to establish what actual conditions might cause failure of the sealing mechanism.