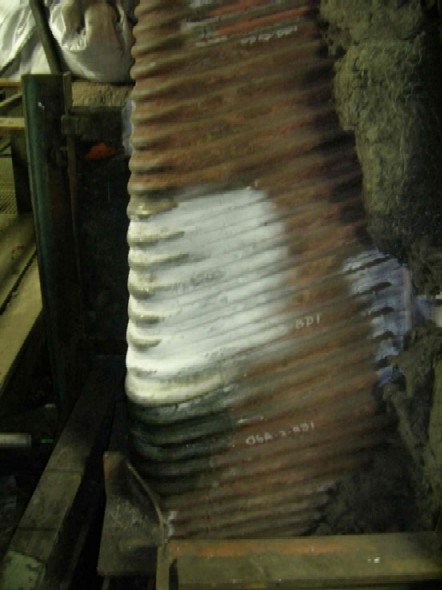
Component:
- Waterwall (evaporator) tubes and bends in two designs of boiler at a European power utility
Problem:
- Multiple failures of waterwall tubing, at straights and bends
- In one case, explosive ejection of tube fragments and a large steam release outside the boiler casing
- Significant downtime at a critical production period
Issues:
- History of corrosion failures in the waterwall tubes and bends
- Safety issues with regard to explosive ejection of tube fragments and large steam releases
- Inspection reveals large number of defects remaining in the waterwall tubes
Objective:
- To determine the relationship between critical crack size and operating pressure
- To establish safe exclusion zones
Approach:
- Fracture mechanics assessment, including leak-before-break analysis
- Steam release calculations
Findings:
- Following hydrostatic testing at ambient conditions (and the inspections undertaken) the maximum current defect size was established
- The failures can be explained solely on the basis of the tube pressure stress and predictions are consistent with the observed failure mechanism and final crack size
- Leak before break analysis provided relationship between operating pressure and critical crack size and hence the likelihood of each failure mode during operation
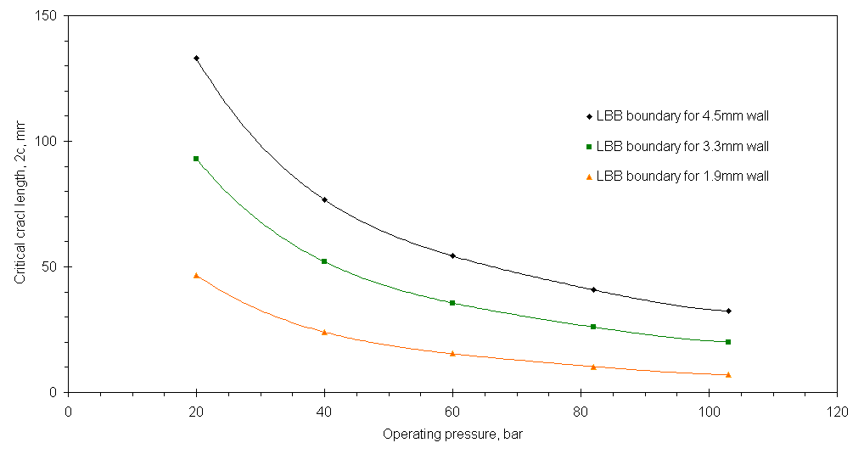
Results:
- Critical crack sizes determined as a function of operating pressure and wall thickness
- Safe operating pressures determined from observed crack sizes
- Standard gas release calculations found to be inappropriate for steam
Safe exclusion zones determined on the basis of more accurate release formulae
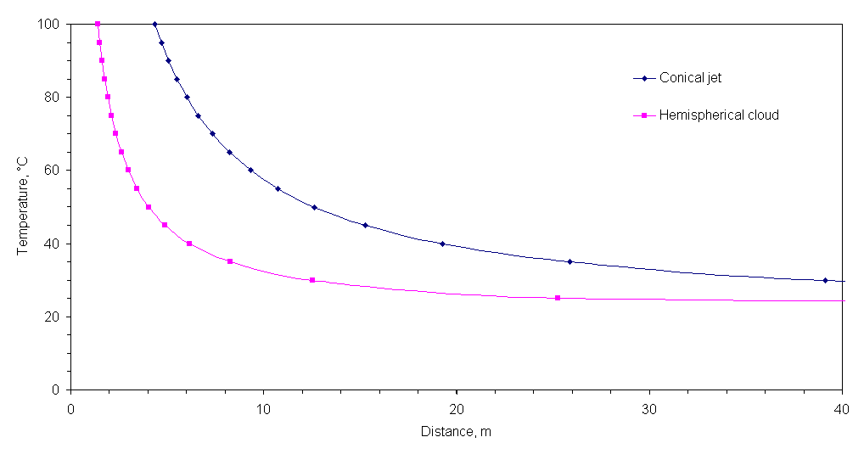
Benefits:
- Explosive type failures can be eliminated by reduced pressure operation
- Unit brought back on-line during critical period
- Fast response by team leads to minimal downtime
- Insurers satisfied by comprehensive analysis undertaken