The objectives of this work were:
- to establish procedures for modelling the residual stress distribution in thick-section PWR pressure vessel welds
- to assess the effects of stress relaxation treatments on welded joints
- to determine the effects of stress relief on subsequent mechanical properties
Finite element models of various thick section components, including selected weld profiles, were created. Techniques to replicate the as-welded residual stress distributions were developed and validated against experimental data. Build up of the weld profile during the welding process was shown to be critical to development of the residual stress distribution which was thus difficult, but not impossible, to replicate.
Application of appropriate creep models enabled assessment of various stress relief procedures. This stress relaxation modelling was successful.
Mechanical tests on material that had undergone a simulated stress relief treatment showed:
- Stress relief damage is detrimental to subsequent tensile strength, tensile ductility, impact strength and impact ductility.
- The effects are consistent and predictable on a loss-of-effective-section basis. Continuum damage mechanics provides a suitable basis for modelling.
- The effects on the brittle-ductile transition are more complex.
- Damage accumulation during stress relaxation is directly proportional to the stress relaxed, and therefore to the plastic strain accumulated. This is consistent with constrained cavity growth.
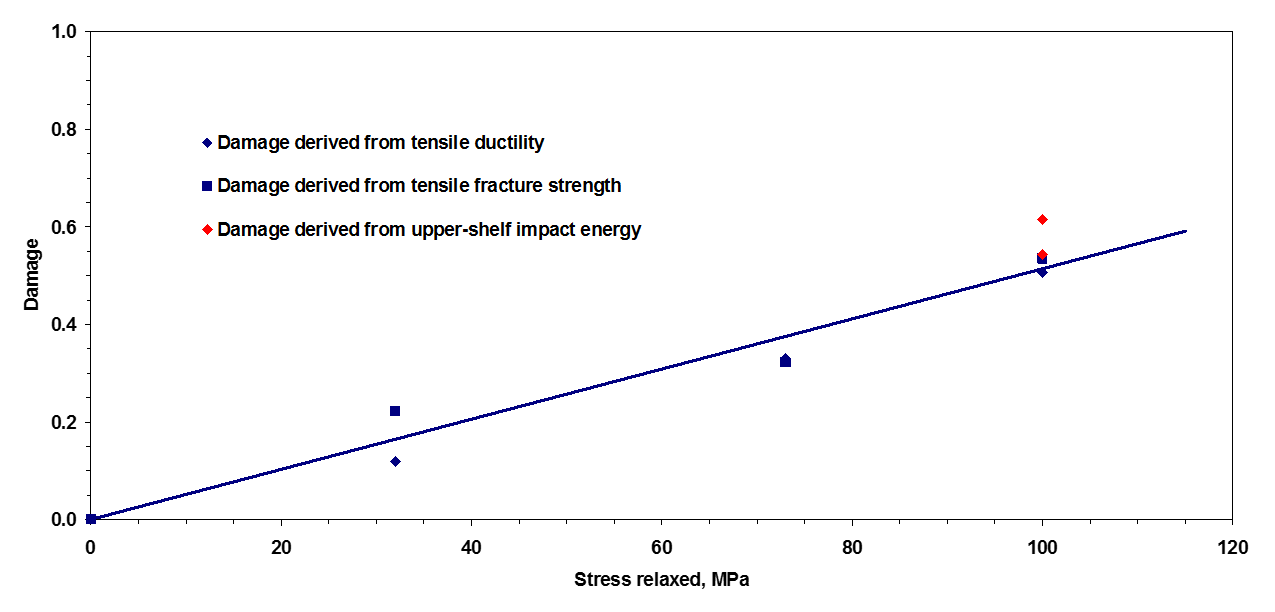
Publications based on this work include:
Brear, J.M.
“Stress relief embrittlement - revisited”
ECCC Int Conf ‘Creep and Fracture in High Temperature Components – design and life assessment’ EMPA, Zurich, 21-23 April 2009
Brear, J.M. and Jarvis, P.
“Living with creep damage… outside the creep range”
Keynote paper at Baltica 7 ‘Life Management and Maintenance for Power Plants’, Helsinki,
VTT Symposium 246/247, Espoo, Vol. 2 pp. 50-64, 12-14 June 2007
Energy Materials, Vol 2, No 2, 2007, pp 109-116