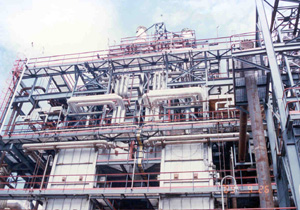
Plant:
- Interconnecting pipework on a Platformer unit at an Australasian refinery, operating in the creep range with a service life of 220,000 h
Objective:
- Formulation of a risk-based inspection and maintenance programme
Approach:
- Classical pipework stress analysis, validated by comparing predicted and observed hot-cold movements
- Probabilistic creep life prediction
- Consequences of failure classified according to sub-component type and fabrication (seam-welded or seamless), on the basis of a leak-before-break analysis. Relative costs assigned by the client
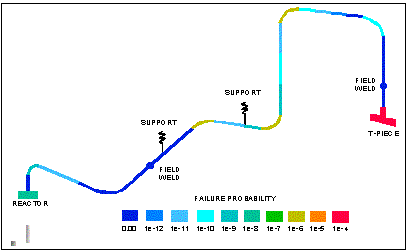
Benefits:
- Critical locations identified on each line
- Failure risk calculated for each location at next four scheduled outages
- Failure risk for each line computed from those for individual locations
- Inspection and maintenance plan formulated and implemented
Published:
Brear, J.M. and Williamson, J.,
“Integrity and life assessment of catalytic reformer units”
Chapter 2 of EFC Publication 42 ‘Corrosion in Refineries’, eds Harston, J.D., Ropital, F.
Inst Materials, Minerals and Mining, London, July 2007, pp 18-46
Barrien, P., Jarvis P., Townsend R.D.
“Risk-Based Inspection and Maintenance Optimisation of High Temperature Plant”
Operating Pressure Equipment Conference. Brisbane, Australia, 7-11 April 1997.