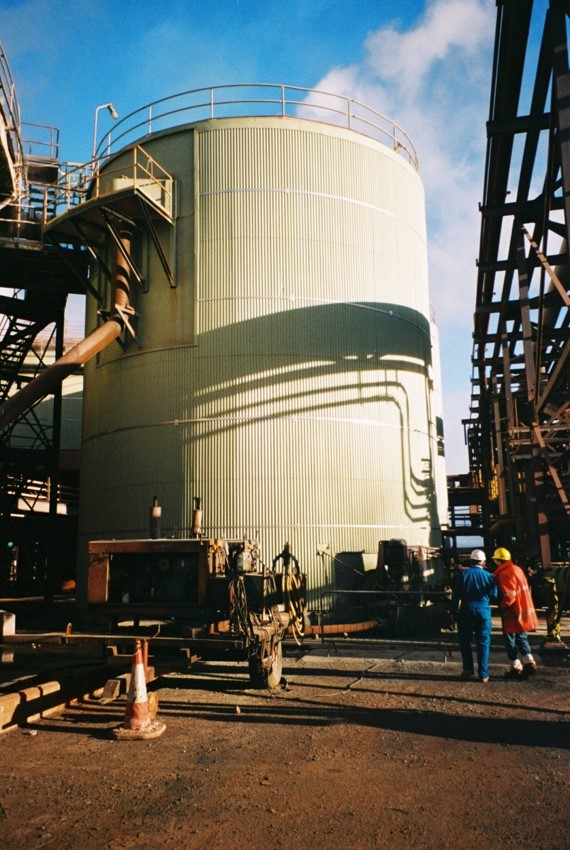
Item:
- 14m high x 10m diameter liquor-decant / wash-thickener tank in an aluminium plant
Problem:
- Current cleaning practice for the tank interior involves personnel access, causing concern for the health and safety management team
- New method proposed to clean the tank using a hydraulic hammer, attached to a 9m long, 1.5 ton hydraulic arm located on the tank roof
- Can the existing tank design sustain the operational loads from the hydraulic arm or are design modifications required?
Objective:
- To determine if the current tank design (to API 650) could support the operational loads of the new method of cleaning and, if not,
- To propose design modifications to allow implementation of the device
Approach:
- Determine the remaining strength in all components of the tank
- Establish the loads arising from operation of the proposed hydraulic arm
- Identify any weak points in the current tank and propose design modification to allow installation and operation of the proposed arm, either by new design or by strengthening of the existing structure
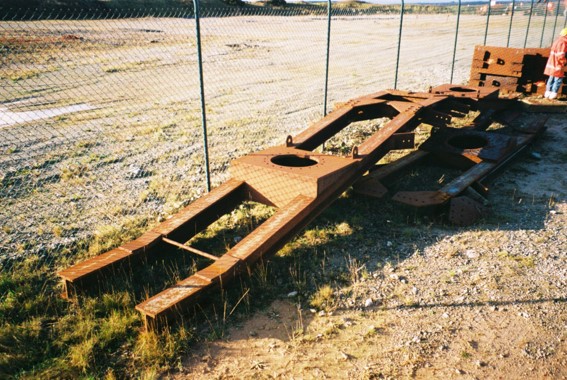
Outcome:
- Analysis concluded that the existing tank roof could not support the operational loads from the hydraulic arm and hammer
- Significant static and bending loads developed during cleaning operation
- Subsequent analysis determined that a new roof structure capable of supporting the loads from operation of the hydraulic arm would be impractical
- Hazard assessment identified that the tank could fail by buckling of the thin-walled shell if damaged by the hydraulic arm, with a possibility of personnel injury
- It was therefore necessary to design a framework capable of supporting the operational loads of the hydraulic cleaning hammer. This must be:
- free standing and not interfere with the surrounding established equipment
- capable of entry into four manholes on the top of the tank
- In partnership with client, initial design of supporting framework proposed
- All operating loads identified and safety factors agreed with client
- Full structural integrity assessment performed
- Detailed sketches provided for manufacturing process
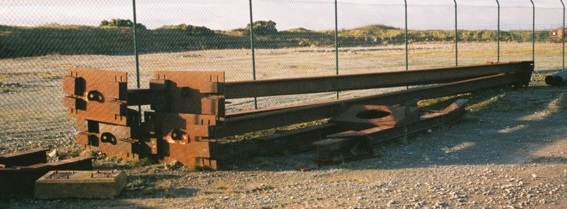
Benefits:
- Design and structural integrity assessment performed in short timescales
- Timely implementation results in cost effective solution for client